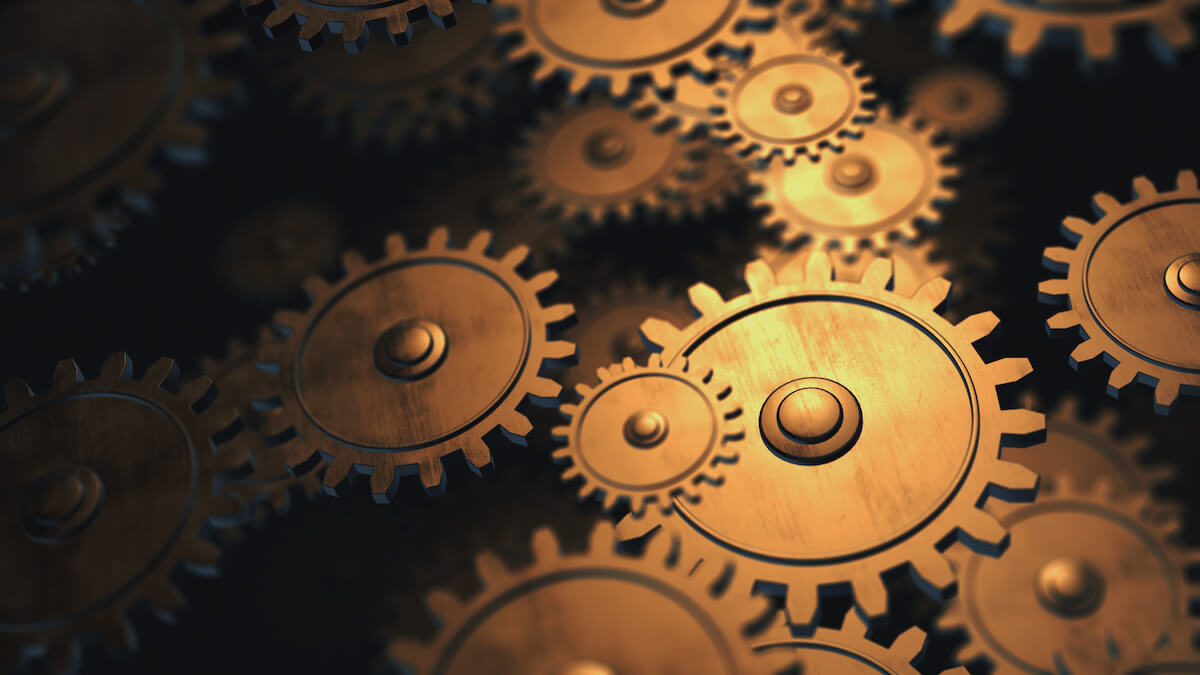
Reduce Time to Market and Prototype Waste
You've Never Innovated Like This Before
The processes your team follows to take a product from concept to production are probably more costly than you realize. With engineering, manufacturing, and quality assurance teams all working in silos at different phases of the process, the lack of consistent data and communication has detrimental results.
The design cycle takes your product from design to testing, but not without multiple iterations. That means your team is spending valuable time and resources on time-intensive adjustments over and over again.
But what if you could streamline that process and reduce time to market by eliminating unnecessary prototype iterations? That’s where Sigmetrix comes in. Here’s how we can help.
Who We Help
-
Give your design team the ability to quickly explore concepts through tolerance models that take seconds, not hours—even the most complex designs.
-
Help team leads gather insights that prototypes can’t usually provide, like realistic assembly process capabilities and “looking inside” the product for root causes of failure in each design.
-
Empower engineers to identify mechanical variation earlier in the design process by creating a more complete tolerance model with the surfaces, construction features, and crude concept geometry that’s more true to life.
-
Shave expenses and add to the bottom line for the entire enterprise by modeling variation, predicting performance and visualizing feature sensitivity for even the most complex systems—without costly physical testing.
-
With consistent data, shared tools, and standardized reporting formats, bring design, manufacturing, and quality teams out of their silos and onto common ground.
How We Help
-
Our solutions allow the consideration of mechanical variation early in the design process, instead of modeling tolerance stacks after the product design and drawings were complete. The bottom line? Drive down manufacturing costs and decrease the likelihood of scrapped parts.
-
Model real-world conditions and make design and manufacturing decisions that aren’t typically possible with prototypes—helping teams reduce time to market by avoiding costly delays and unnecessary iterations.
-
Design teams can take their biggest ideas to the prototyping phase, even without derivative design and manufacturing processes that offer years of empirical data to predict performance.
-
Generate a tolerance model report in seconds by taking even the most complex models from systems like Creo right to EZtol via a simple, out-of-the-box plugin.
How You Can Save Time With Sigmetrix
Understand the ways our GD&T and tolerance analysis softwares can reduce time to market by expediting the product lifecycle.
Sigmetrix provides simulation tools and training that enable design teams to build tolerance models that more accurately predict and simulate real-world behaviors in equal or less time than it takes to populate a stack-up spreadsheet. Designs can finally go from engineering to manufacturing with accurate tolerance values, no unexpected variation, and no costly loopback in the design process.
Traditional stack-ups can require completed drawings or costly prototypes, which means no tolerance analysis until the design is already done. Teams go back to square one when stack-up reveals problems, wasting time and money. With Sigmetrix GD&T simulation tools, engineers and designers can quickly build and compare concepts with simple CAD models and construction geometry. Consider mechanical variation early on without complex mathematics and unknowns about the assembly and inspection processes.
Along with being costly and rife with limitaitons, physical prototypes can’t provide a statistically significant sample size that represents the production volume of the final product. They don’t always represent realistic process capabilities of manufacturing. And they don’t allow your team to “look inside” the product to determine the root cause of failure in critical requirements. But with our simple-to-use software, you can model real-world conditions that simulate the impact of variation without the need of physically building a prototype. Inform crucial design and manufacturing decisions before you’re even out of the prototype phase, and avoid costly rework.
It’s not possible to take every design concept all the way to prototyping, but what if it were a lot simpler to get the kind of feasibility data you needed quickly? With Sigmetrix’s simple software, you can model variation, predict performance and visualize part and feature sensitivity for complex systems without expensive physical testing.
Industry Leaders Using Sigmetrix to Beat Their Competition to Market
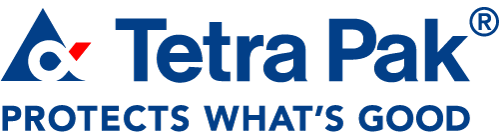
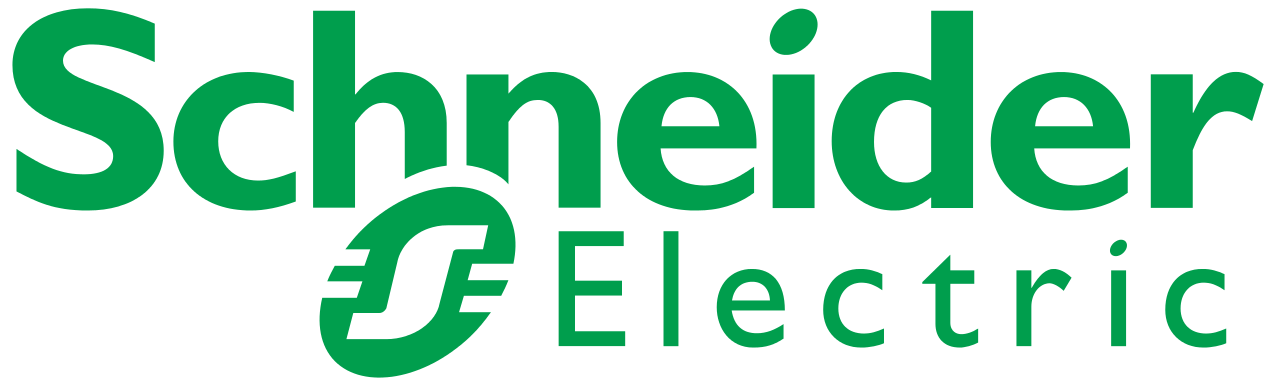



Save Time on Prototyping Cycles With Better Tolerance Analysis Software
Sigmetrix offers a suite of services to meet your team’s specific needs. If time to market for new products is slowing you down, explore these software options or schedule a demo.
How Sigmetrix Helps Across the Enterprise
Save time, improve profitability, innovate more, and maximize return on your investments across the enterprise.
Read Expert Views on Faster Tolerance Analysis
Learn from our experts and start improving your design and prototyping cycles.
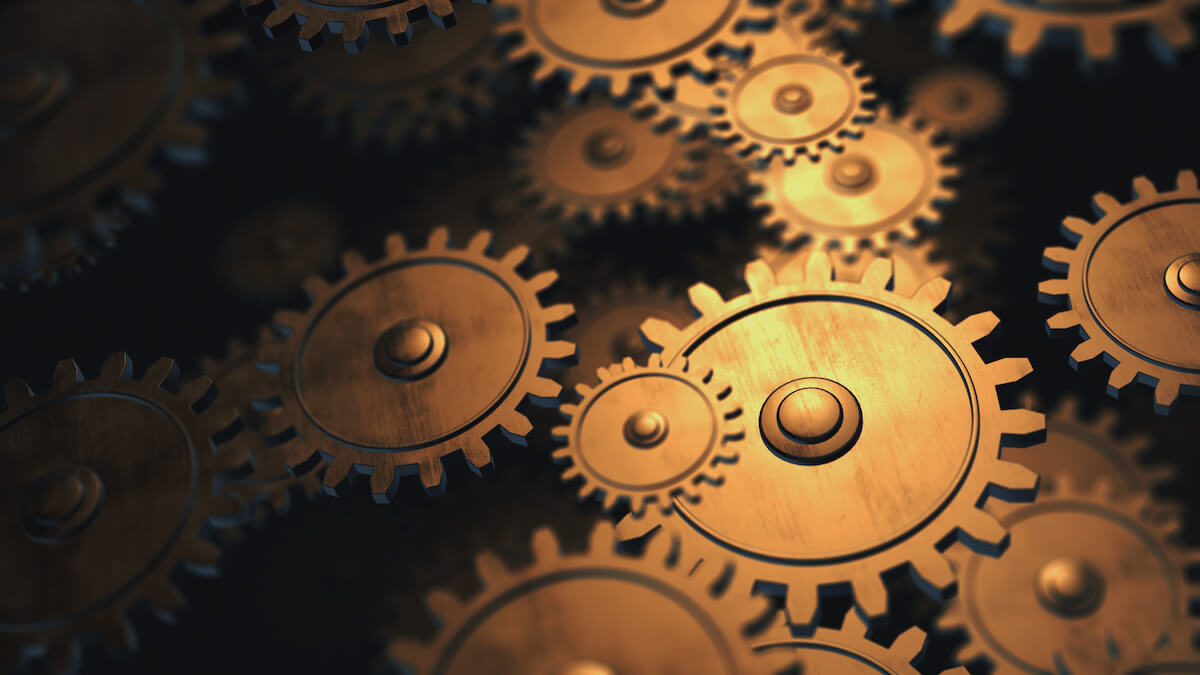
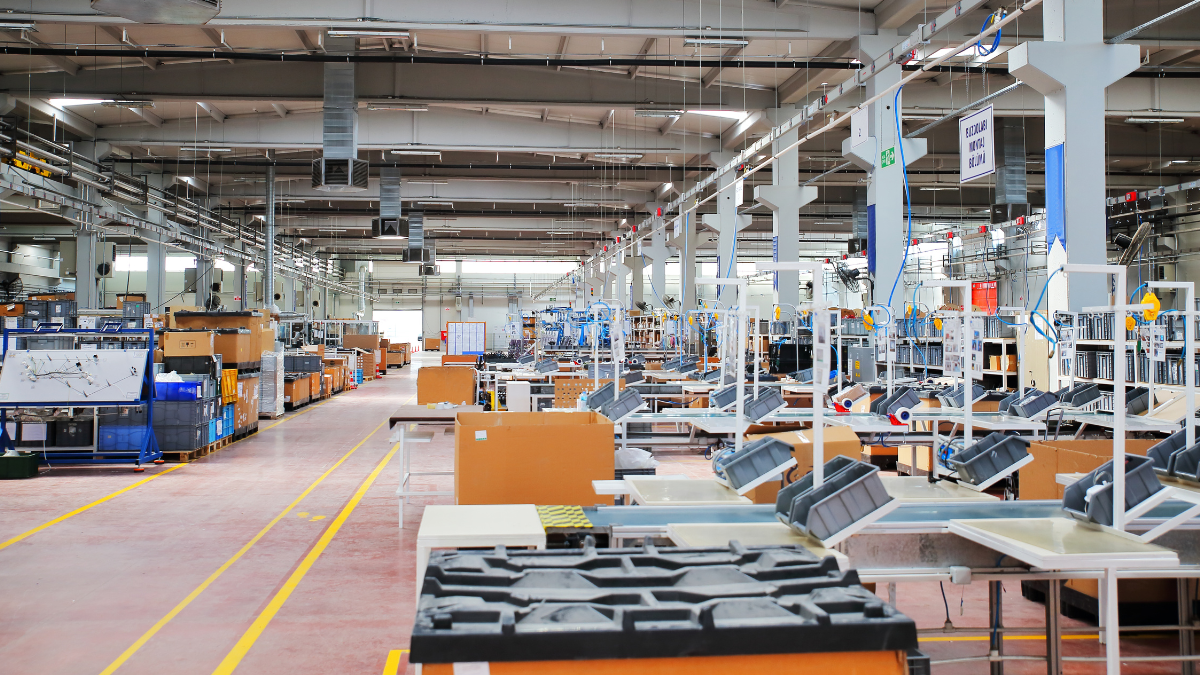