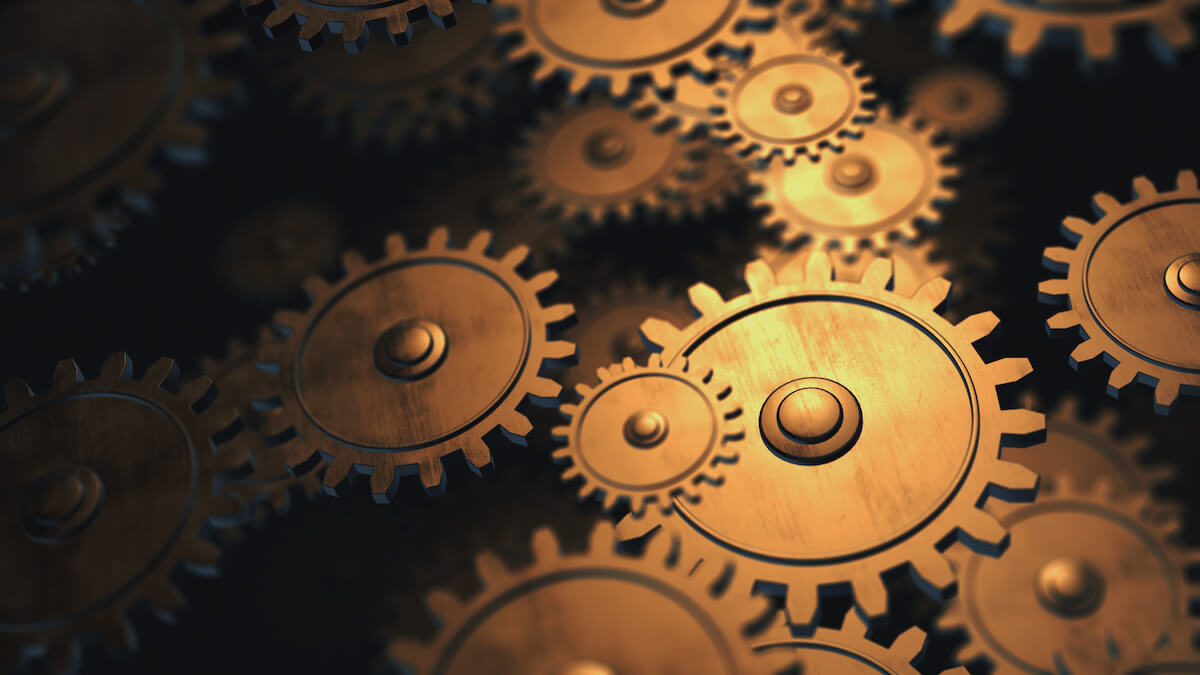
Deliver More Innovative Products Through Better Mechanical Variation
Deeper Understanding of Mechanical Variation to Develop Innovative Products
Product and process innovation will always be critical to the long-term success of any organization. And industry leaders see the major benefits of incorporating manufacturing and quality engineers early in the development process.
However, it’s historically been cumbersome to manage variation within this process—it requires a great deal of work, insight, and setup that can become institutionalized in spreadsheets or design patterns. These templates become rigid by nature, and innovation is stifled because updates must fit within the confines of these internalized tools. Making changes could require changing the tools themselves, which causes time-intensive rework.
Sigmetrix’s software frees up engineers from the confines of internalized rigidity by providing access to variation insights quickly. Innovation isn’t halted by traditional tolerance stack-ups performed once the design is complete, and the ability to quickly simulate sensitivity to variation in concepts leads to more innovative, breakthrough products. With groundbreaking GD&T and tolerance analysis software, formerly siloed teams can collaborate throughout the design cycle to check product feasibility, easily and inexpensively compare multiple concepts, and analyze even the most complex iterations with more insight than a physical prototype allows.
Stop stifling innovation and empower your teams to develop your next breakthrough product.
Who We Help
-
Satisfy and exceed company growth goals with better product ideas and new market potential.
-
Enable engineers to build upon new concepts with a concrete understanding of product feasibility early in the design process.
-
Give innovative teams a better way of doing tolerance stack-ups that don’t break internal spreadsheets. Instead, they can be done quickly, easily, and accurately in a shared software for faster iterative testing. Not only that, design teams can take 1D stack-ups to 3D visualization more seamlessly than ever.
How We Help
-
Get feasibility data faster than ever without investing the time and resources to take a creative notion all the way to prototyping.
-
Gather insights that allow teams to select the most robust product or process designs for continued innovation, even when it’s not intuitive, through built-in software features like sensitivity animation.
-
Break out of internal tolerance analysis spreadsheets and rapidly model new ideas in a 3D environment to understand how variation impacts the design.
How to Improve Product Innovation With Sigmetrix
Our GD&T and tolerance analysis software makes mechanical variation management an integrated part of the innovation process, not an afterthought that derails creativity.
Consider mechanical variation early on, even without complex mathematics and unknowns about the assembly and inspection processes. When needed, our stack-up software allows you to build and compare concepts with minimal geometry, so your team can figure out what’s possible earlier in the concept design loop and stop wasting valuable time iterating on concepts that would be too costly or impossible to produce.
Many companies have developed internal spreadsheets or tools that allow design engineers to enter the dimension loop and tolerance values for their design projects and determine if the tolerance values are acceptable. Although these internally developed tools are only 1D, they overcome this limitation by including assumptions based on years of empirical data and hands-on observations. While these tools can be very accurate and reliable if the critical interfaces and interface geometry doesn’t change, it limits innovation to derivative products. Engineering teams become dependent on these structured tools and, subsequently, their legacy designs.
New ideas, such as those that require geometrically unique interfaces, are discouraged because the internal tools can’t accommodate them. Innovation is slowed or stifled completely. The solution? Using Sigmetrix to give engineers the knowledge of how variation impacts their design, the tools to quickly and easily simulate that design in a 3D environment, and the ability to break out of the costly derivative-only mindset.
Prototype, pilot, and test builds can provide valuable information during the development of a new product.
However, physical prototypes have limitations. They don’t typically allow your team to “look inside” the product and determine how part features interact in the real world. They don’t reveal non-intuitive effects of the design on critical-to-function specifications. They don’t always help the engineer understand why the design is acting the way it is. And most importantly, they don’t allow for the essential, quick “what-if” testing that often leads to innovative breakthroughs.
Sigmetrix gives your organization the ability to model your product and process design ideas and investigate the model to see the outcome.
Part of the innovation process is suggesting ideas that seem to push the envelope almost too much. It’s not always possible to take these concepts all the way to the prototyping phase due to cost and time requirements, but this leaves valuable learning and possible winning ideas on the cutting room floor.
But what if it were a lot simpler to get the feasibility data you needed quickly and inexpensively? Sigmetrix allows your team to model variation, predict performance and visualize part and feature sensitivity for complex systems without expensive physical testing.
These Sigmetrix Customers Are Evolving Without Burning Time and Resources
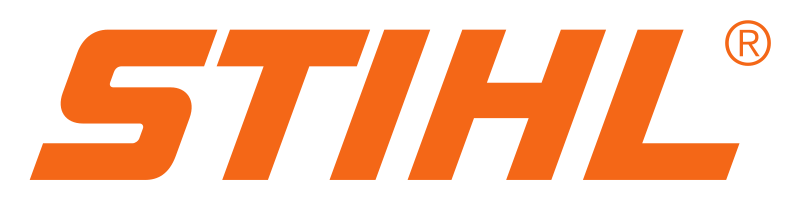
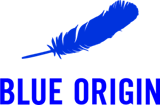
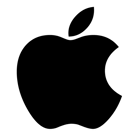
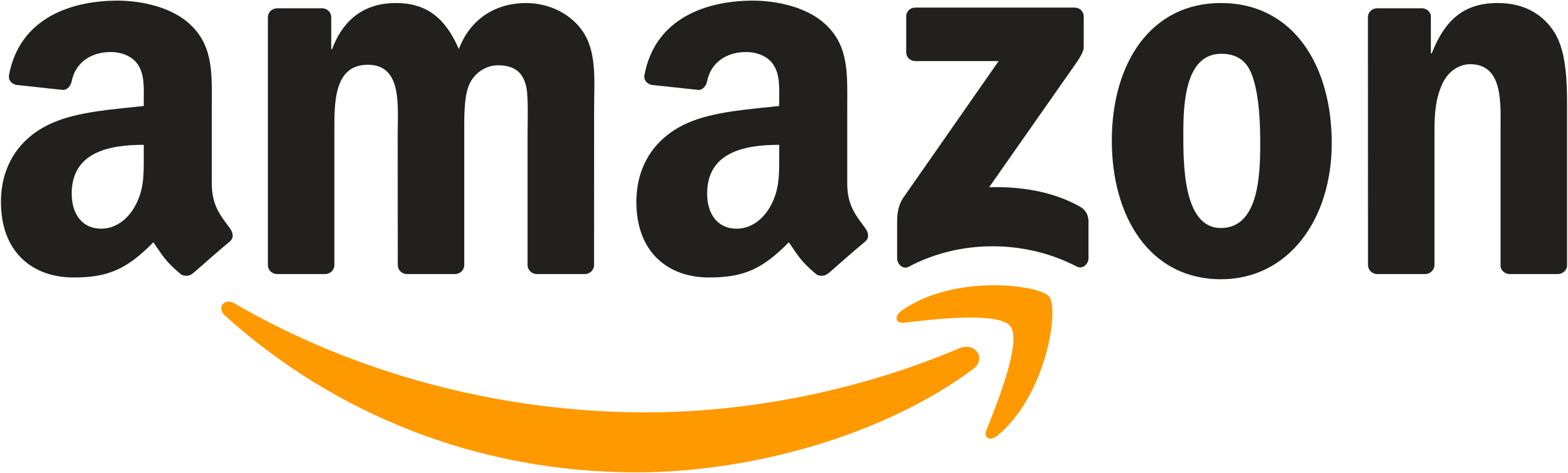
Tolerance Stacking and GD&T Software That Enables Creativity
Break out of the legacy tolerance value spreadsheets and give engineers the knowledge of how variation impacts their designs—with 3D simulations that eliminate the constraints currently stifling your organization’s innovation.
How Sigmetrix Helps Across the Enterprise
Save time, improve profitability, innovate more, and maximize return on your investments across the enterprise.
Learn From the Experts in Product Design, Engineering, and Manufacturing
Discover helpful resources on our blog.
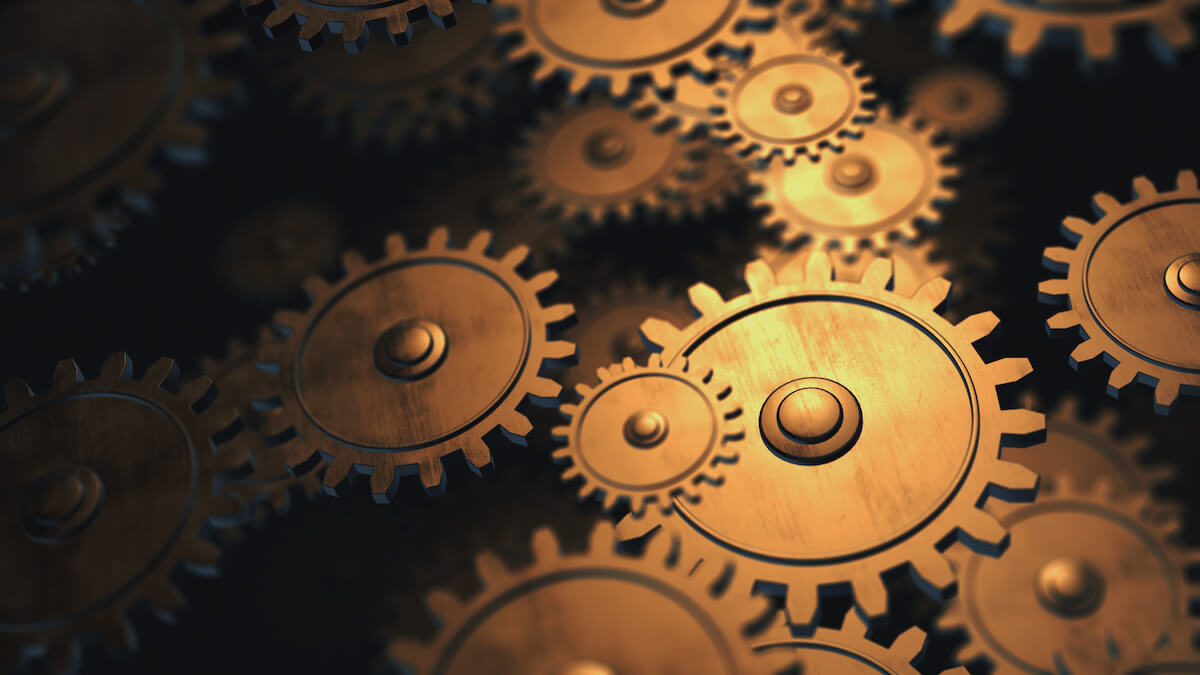
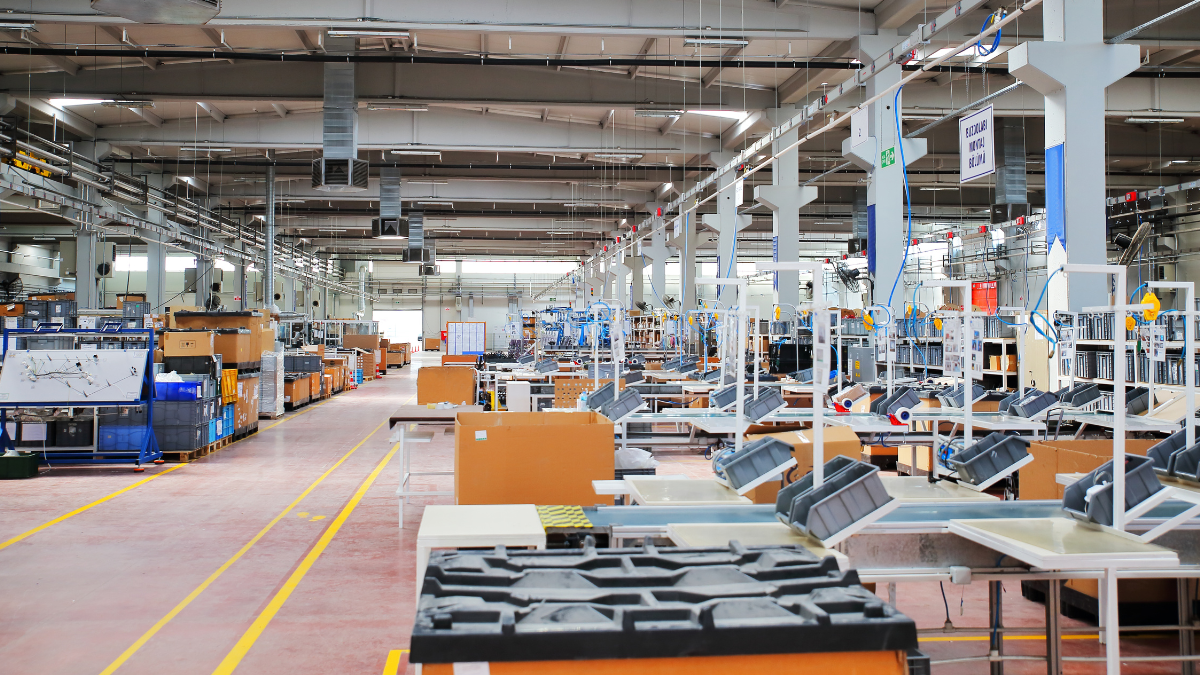