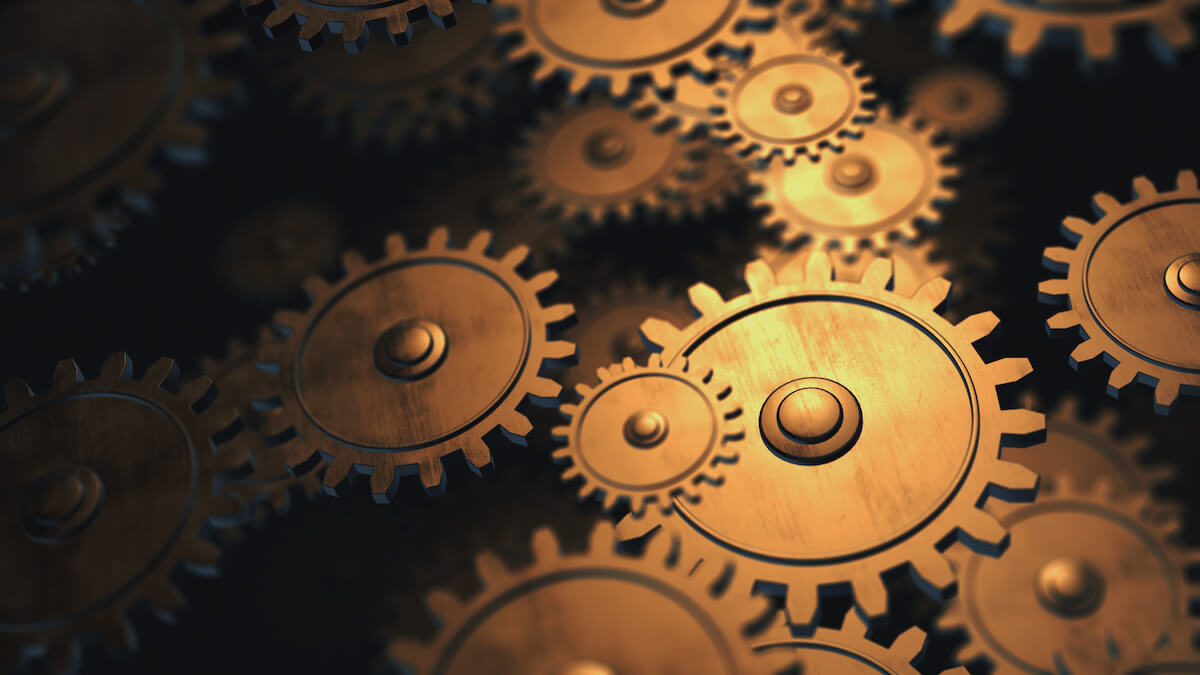
Better Profitability Balancing Product Quality & Manufacturing Costs
Manage Mechanical Variation for Higher Quality, More Profitable Products
Mechanical variation is inevitable. However, reactively addressing mechanical variation issues leads to additional costs, lowering overall profitability. Not addressing mechanical variation issues when they’re detected or completely missing them altogether lowers product quality and, in turn, can impact company reputation, leading to less revenue.
Proactive mechanical variation management can be a reality with Sigmetrix. Our tolerance analysis and GD&T solutions drive profitability across the product development cycle, resulting in higher quality and lower costs across a product’s entire lifespan. Our solutions help companies optimize their manufacturing processes, enabling more efficient decision-making across the enterprise, which leads to notable product quality improvements without driving up costs.
Who We Help
-
Give product designers the ability to visually and graphically understand how variation impacts product performance—before time and resources are wasted on production.
-
Provide engineers visuals that assist in understanding the relationship between the input versus output of designs, identifying variation issues early on in the design process.
-
Help manufacturers apply product capability data to make informed decisions on when to use precise, expensive processes and where they can drive cost-savings.
-
Assist engineering with cost-reduction efforts by determining where tolerances can be loosened, analyzing the impact of replacement parts on product quality, and highlighting opportunities for improvement.
-
Give designers and engineers the ability to determine if out-of-spec parts are acceptable.
How We Help
-
Prevent costly rework by identifying and meeting requirements early on in the design and manufacturing processes.
-
Gain feedback on your GD&T early and often to achieve high product quality before prototyping or production starts.
-
Understand mechanical variation and how it affects critical product characteristics while visualizing high-impact sensitivities for better design decision-making and more robust products.
-
Model dimensioning schemes, edit tolerance values, and obtain results with easy-to-use tools linked in an environment that is similar to your existing workflow.
-
Get ahead of mechanical variation problems to effectively manage them during manufacturing and assembly.
-
Gather and understand data on corrective actions like out-of-spec part usage or reworking.
-
Provide a consistent approach across the enterprise between contributors and consumers of GD&T.
Want to See How Sigmetrix Helps Balance the Cost & Quality of Your Products?
Let us show you around. Book a discovery call today.
How Sigmetrix Helps You Build Better Products, While Driving Profitability
Understand how to strike an optimal balance between product quality and manufacturing costs by facilitating precise tolerance analysis and managing mechanical variation.
Understanding how dimension sensitivity contributes to product characteristics is a key first step to managing mechanical variation.
Sigmetrix empowers engineers and designers to analyze, anticipate, and address manufacturing variations early in the product concept and design process. This proactive approach ensures that designs are more resilient to variation and reduces rework in the manufacturing process, ultimately resulting in more robust, cost-effective, and reliable products.
Sigmetrix’s tolerance analysis solutions identify how variations in individual design characteristics affect critical product features. They demonstrate visually and graphically how variation can affect a product’s performance, allowing the user to target key contributors to improve design robustness.
When engineers and designers create a product, they're often figuring out how to control its features for the best quality, and also how to apply the proper dimensional values to guide manufacturing. The tricky part? All too often, without simulation software, they don't get crucial feedback until they've already made prototypes or started production. This leads to unprofitable processes, waste, and rework.
Sigmetrix accelerates the design and development iteration process by evaluating how a change in design impacts quality before production. Engineers can quickly navigate through various dimensional control options, refining designs to achieve the desired quality standards in a shorter time frame. This allows for more efficient, cost-effective adjustments long before designs are sent to manufacturing. The best part? Sigmetrix offers your team a familiar environment to model dimensioning schemes, easily edit tolerance values, and obtain results faster than ever before, without disrupting their workflow.
Mechanical variation is inevitable. How your company handles that variation can make or break your profitability. You have choices: Test many prototypes, fix issues immediately upon inspection, predict and analyze, and more. Many of these options can have a negative impact on both efficiency across the product development cycle and your bottom line.
Sigmetrix’s tolerance analysis and GD&T solutions equip businesses to proactively manage mechanical variation from conception, ensuring continual control throughout manufacturing and assembly. Our solutions use sensitivity and contribution data to help identify potential sources of quality issues, along with manufacturing capability data to make appropriate process selections. This approach enables anticipation and prevention of variation issues, avoiding reactive, high-pressure, and high-cost corrections.
In the production phase, encountering parts that deviate from initially specified tolerance limits is a common occurrence, and out-of-spec parts cannot be accepted without authorization. This leads to rework to get the part in spec or scrapped altogether—both leading to extra expenses.
Sigmetrix provides advanced analysis tools that assess the impact of out-of-spec parts on the overall product based on actual production data . Our tolerance analysis solutions quantify the impact of dimensional variations on part functionality, and that data can then be used to influence design change orders to make sure the proper actions are being taken to fix the product. This enables engineers to prioritize corrective actions versus rework, and helps them understand how functionality, assembly, and quality could be impacted based on the severity of deviations.
In an effort to achieve engineering excellence, analyzing factors like part wear, the impact of sustaining actions, supplier changes, and tolerance optimization is key. For instance, understanding how part wear affects variation helps in predicting and managing potential deviations over the product's lifecycle, ensuring sustained quality and reduced rework or replacement costs.
Sigmetrix solutions predict how part wear affects dimensions, analyzing the impact of sustaining actions on product quality, predicting dimensional variations due to supplier changes, and providing tools for comprehensive tolerance analysis to optimize without compromising quality. Our tolerance analysis and GD&T solutions enable efficient design iterations, precise tolerance management, proactive root cause analysis, and ongoing design improvements, reducing lifecycle costs and optimizing manufacturing processes.
Across the enterprise, there are many teams that interact with, contribute to, and consume mechanical variation information. And making sure that everyone is relying on and understands updated, consistent information is crucial to avoid mistakes and wasted time.
With our training and consulting services, Sigmetrix helps assess the maturity of your organization’s technical variation management. We provide a consistent approach and language in training, knowledge resources, and tools across the organization. We help standardize data and reporting formats to improve communication and integrity of digital threads across the enterprise. Our tolerance analysis and GD&T software solutions also provide contextual in-tool guidance that augments training. This enables users to quickly figure out what's causing variation issues, like part wear or assembly problems, and simulates solutions to fix them, saving time and money.
Industry Leaders Using Sigmetrix to Create Better, More Profitable Products
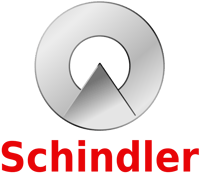
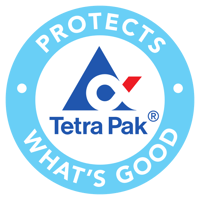
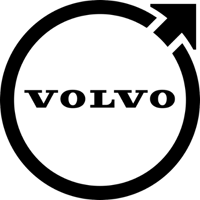
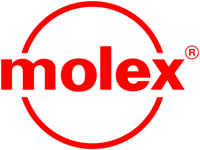
Maximize Quality Excellence and Unlock Cost Savings
Our tolerance analysis and geometric dimensioning and tolerancing softwares ensure precise design control, optimized tolerances, and streamlined manufacturing processes, leading to higher-quality products and improved profitability through reduced costs and increased efficiency.
How Sigmetrix Helps Across the Enterprise
Save time, improve profitability, innovate more, and maximize return on your investments across the enterprise.
Get Expert Resources to Improve Your Processes for Better-Quality Products
Learn from our experts to help transform your manufacturing process into both a quality- and profit-driving machine.
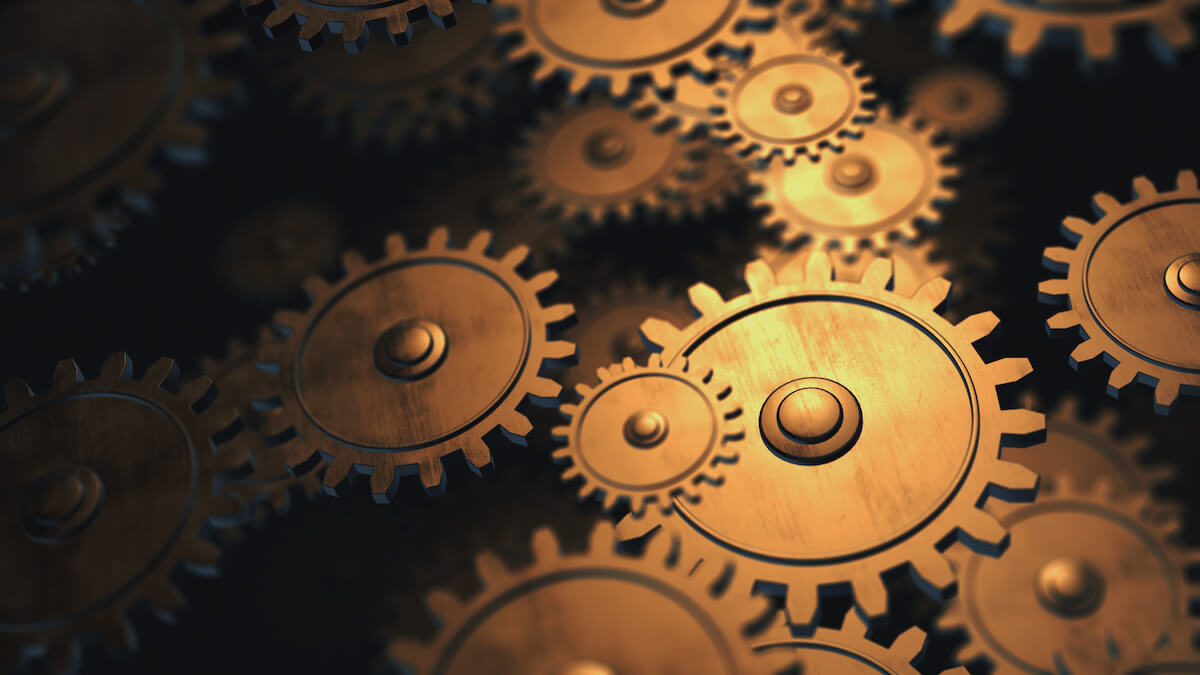
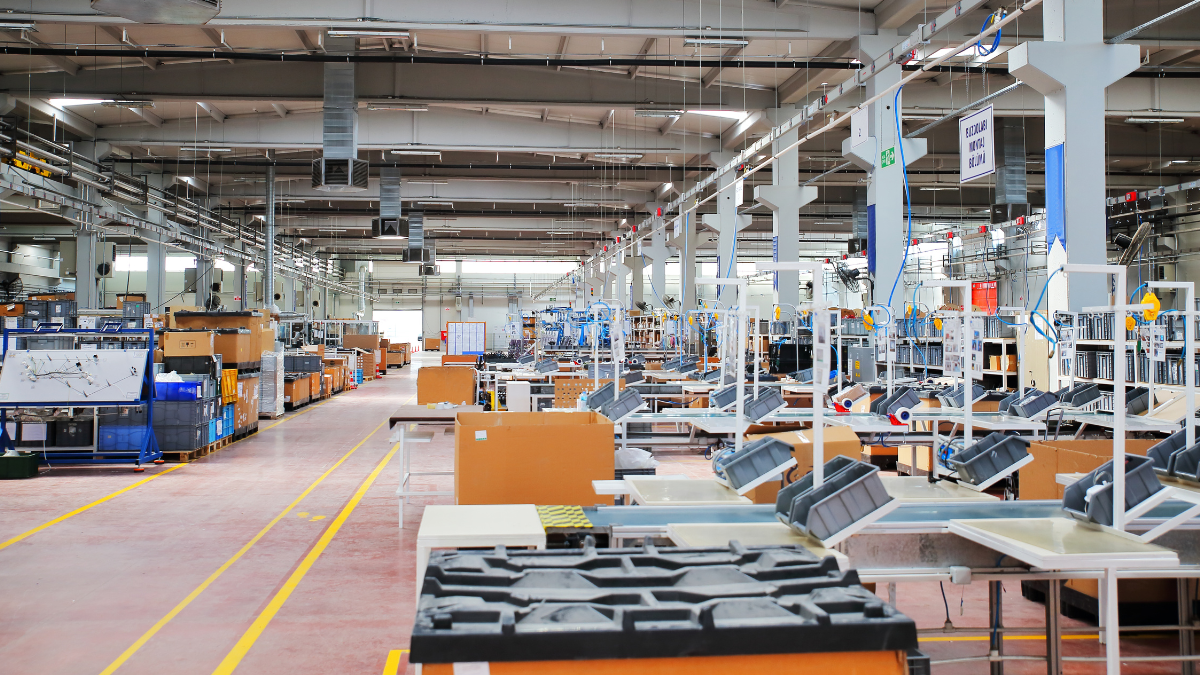