Industry Applications
Some of the Industries We Serve
Sigmetrix tolerance analysis and GD&T software solutions help engineers, designers and product managers from a variety of industries bring robustness and accuracy to their designs, significantly improving product quality while drastically reducing production costs. For industry-specific tolerance analysis and GD&T application examples and case studies, please select from the following:
- Automotive
- Med Dev & Pharma
- Aerospace & Defense
- Electric Power Distribution
- Electronics & Communication
- HVAC & Appliances
- Pumps & Compressors
Automotive
Precision is the engine that drives reliability. The application of CETOL 6σ in the automotive industry provides a powerful example of the successful use of Sigmetrix’s tolerance analysis and GD&T software solutions.
Key projects:
-
Powertrain
-
Chassis
-
Electrical
-
Interiors
-
Body/Vehicle Engineering
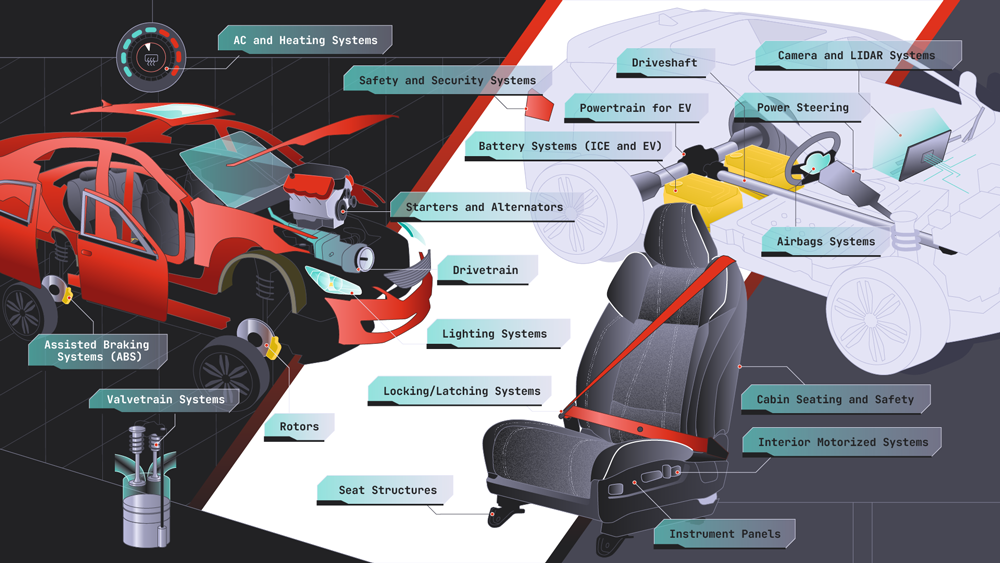

Medical Dev & Pharma
It’s all about controlling the design and Staying Out of the News! Medical device companies recognize the need for accurate, precise tolerance analysis and GD&T solutions. Utilizing Sigmetrix’ CETOL 6σ and GD&T Advisor products empower our customers to:
- Comply with increased regulatory requirements
- Products are predictable and inherently safe
- Validate software tool internally
- Allow for easy reporting
- Balance quality and cost
Because of the unique regulatory requirements and significant liability issues inherent in many markets today, the more visibility a medical device engineer has into the actual performance of the design after manufacturing, the greater his ability is to control risk via the design and minimize liability exposure.
Medical device companies recognize the need for accurate, precise tolerance analysis solutions. Medical device industry customers consist of leaders in the following areas:
-
Blood monitoring and diabetes care
-
Imaging
-
Implantable devices
-
Orthopedic and spinal implants
-
Surgical instruments
Aerospace & Defense
It can be really difficult to repair a satellite that’s already in orbit, a weapon that’s in use in the field, or the landing gear on a jet that took off hours ago. The aerospace and defense industry represents one of the biggest sectors that Sigmetrix’ serves. Our CETOL 6σ tolerance analysis and GD&T Advisor products enable some of the industry’s leading companies to expand their precision assembly engineering and design tolerance analysis all the way from early concept design through inspection, providing product development teams the ability to deliver higher-quality and more precisely engineered products.
Key projects:
-
Satellite systems
-
Landing gear
-
Missile systems
-
Optics
-
Weaponry
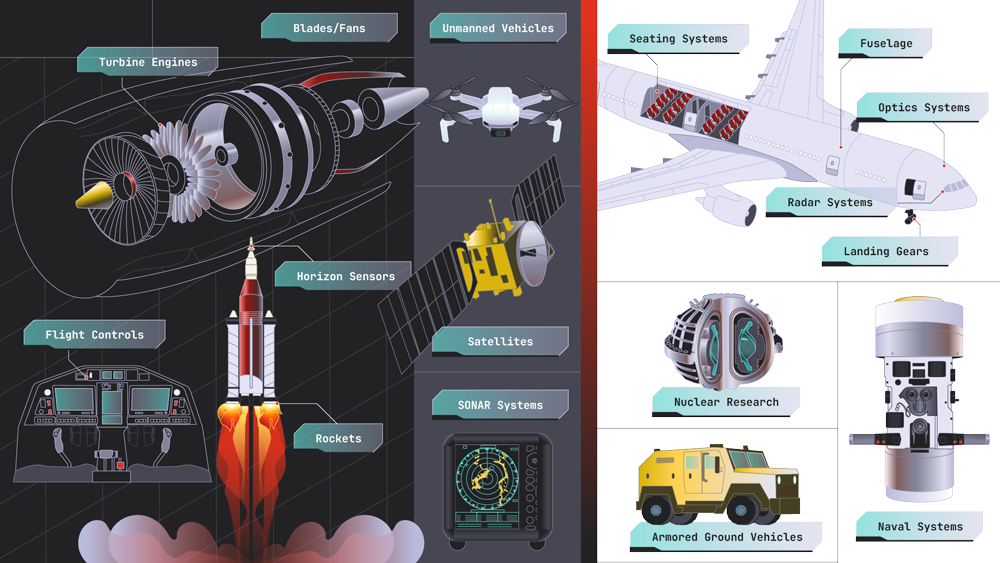
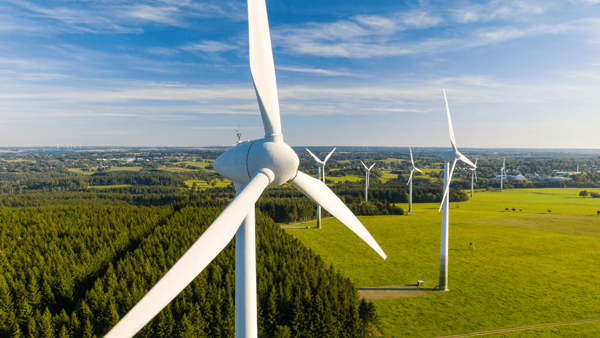
Electric Generation Distribution
Energy generation, distribution and maintenance are key when trying to supply power to cities, allowing vehicles to run on just electricity, supplying power to regular household electronics and more. When trying to adhere to strict regulatory standards for production, understanding how your products are manufactured and will fit together is critical to success.
Production flexibility and failure reduction are hard to achieve when manufacturing products with complex variation data. Sigmetrix visualizes and simplifies variation data to provide key analytics, helping to capture and share critical information that reduces waste while increasing product flexibility.
-
Circuit Breakers
-
Windmills/Wind Energy
-
Electric Motors
-
PCB
-
Batteries
-
Pins and Connectors
Electronics & Communication
Using Sigmetrix’ tolerance analysis and GD&T software solutions early in the consumer products design process and concept stages enables designers and engineers to recognize potential problems, find a better design, and produce more reliable, higher-quality products at a lower cost, with dramatically reduced recall and warranty issues.
In the consumer products industry, warranty issues and product recalls are always in the back of designers and manufacturers’ minds. Improving the design and manufacturing processes helps ease those worries. An effective tolerance analysis forecast & review helps ensure that the specifications mandated during the design phase will work down the line in manufacturing, and that the end result – the product, will not only satisfy the consumer’s needs but will do so for the required amount of time at an effective cost.
Key projects:
-
Printer cartridge
-
Cellular phone
-
Camera focus
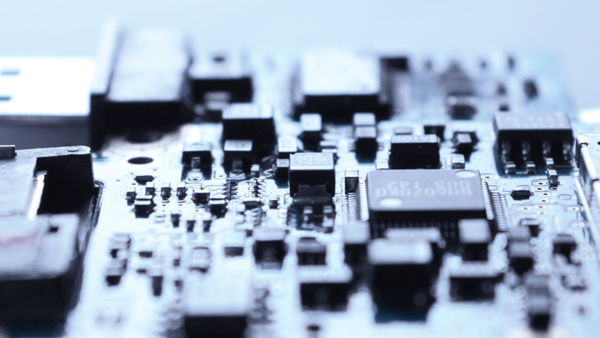
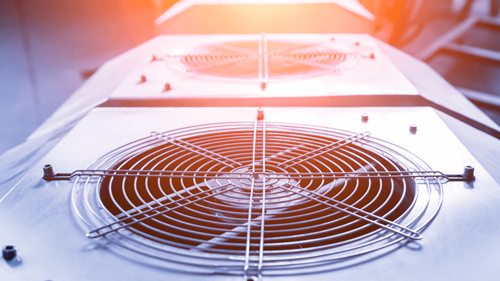
HVAC & Appliances
Keeping your cool in the HVAC industry is no easy task. With warranty and quality issues always in the picture, industry leaders use CETOL 6σ software for assembly variation & GD&T analysis, to save hundreds of thousands of dollars every year by creating more robust, reliable designs. Engineers & parts manufactures depend on GD&T declarations to ensure parts assembly and warranties are viable for longer periods of time. By identifying the tolerances of various parts during inception and prototyping time to production and final product reduces costs and long term maintenance expenses.
-
HVAC Door Seal
-
Automotive HVAC Mechanism
Pumps & Compressors
When it comes to moving fluids and gas, relying on the tools being utilized to perform their job is critical. Sigmetrix allows the visualization of worst-case scenario simulations, gap analyses and more key metrics before a design is ever sent to production, ensuring that the final product meets the required standards. Identifying and acting on design flaws before production isn't just a time-saver, it can be a life-saver.
-
Hydraulics
-
Ball Valves
-
Oil Pumps
-
Flow Meters
-
Air Compressors
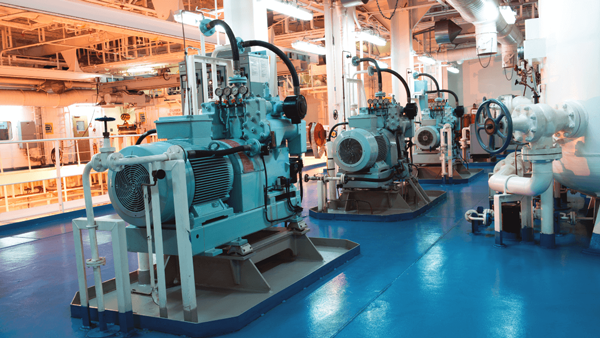
Resources to Help You Master Mechanical Variation Management
Here’s How Companies Like Yours Use Our Tolerance Analysis Solutions
OUR CUSTOMERS ACROSS INDUSTRIES
Customers Who Trust Sigmetrix
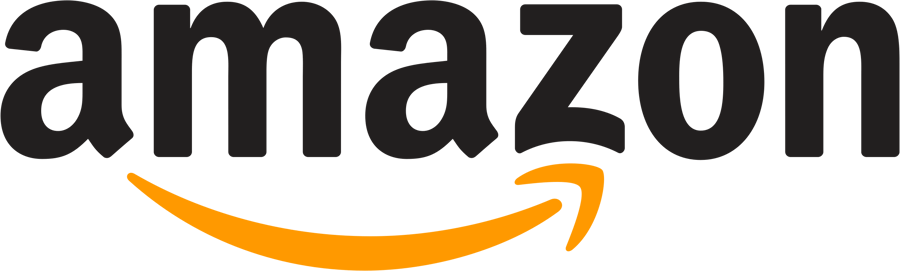

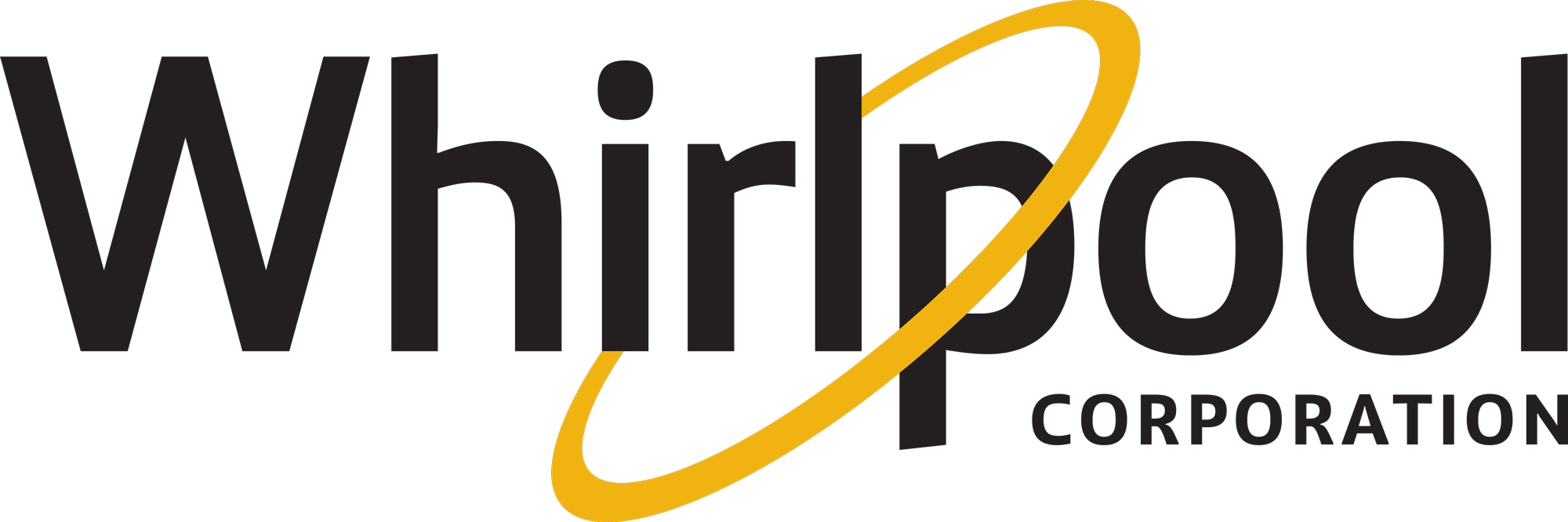



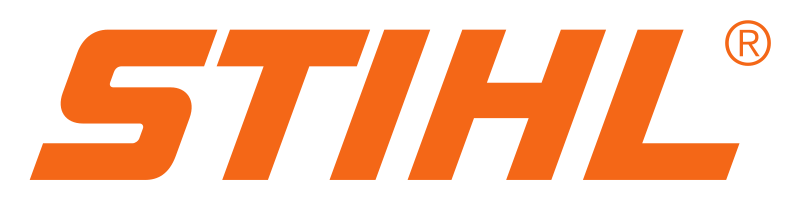
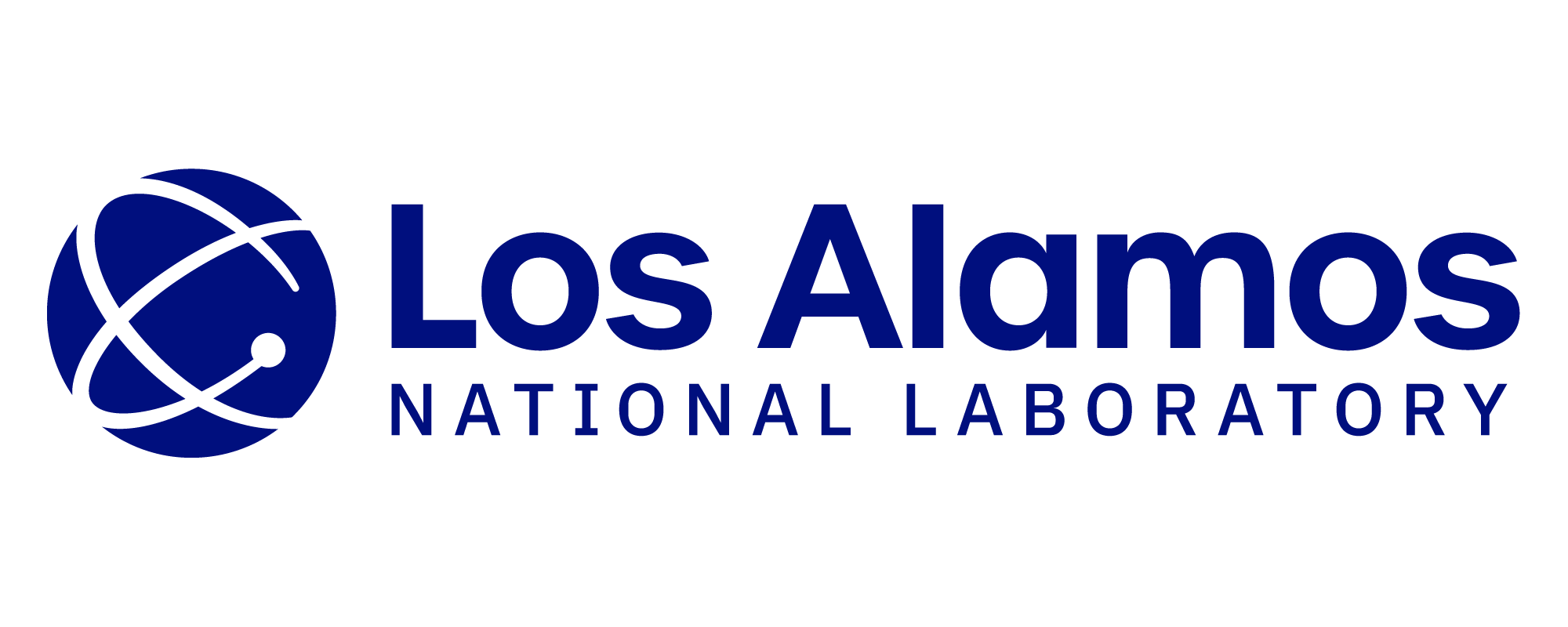
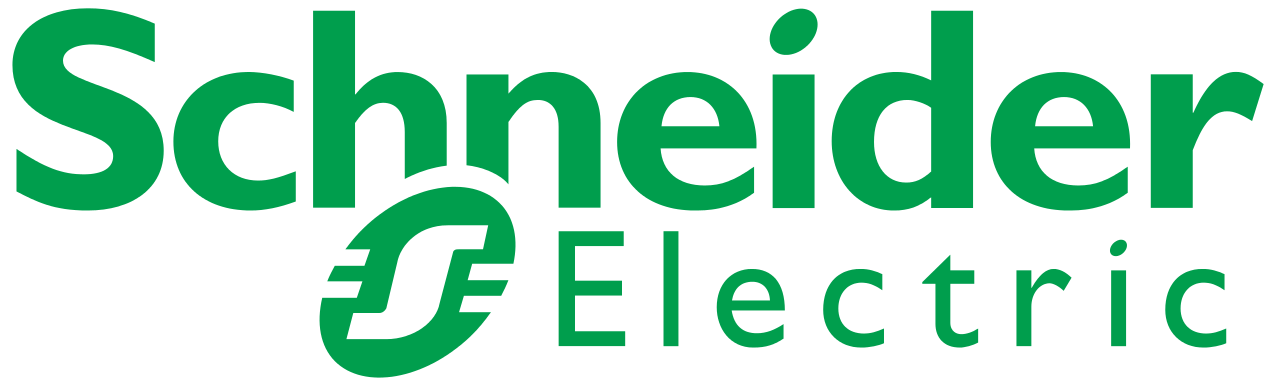